Company Profile
Initial Production Checks (IPC)
The IPC is conducted as soon as the manufacturer has started production and has 50 – 100 pieces completed and ready for packing. The purpose of the IPC is to determine if the initial batch of products produced by the manufacturer complies with the client’s specifications. If at this stage, any deviation beyond established tolerance is noticed, timely corrections are made, before bulk production begins. A written inspection report is prepared, confirming observations and a copy is given to the manufacturer. If required a copy can also be sent to the customer.
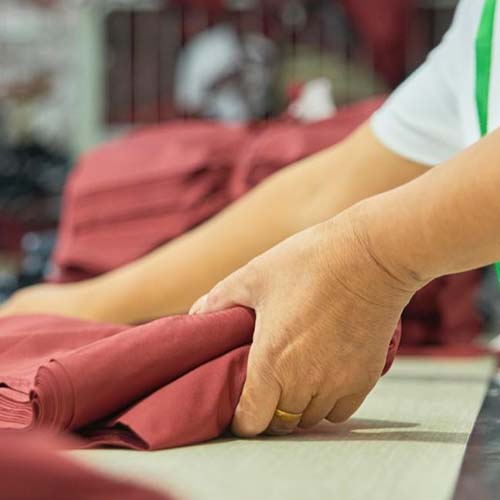
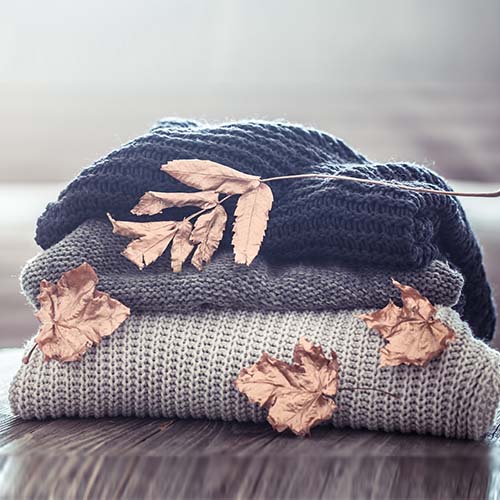
Mid Production Checks (MPC)
The MPC is conducted a few days after the IPC, particularly when decencies have been found during IPC depending on the shipment date. For large orders MPC are performed. The MPC is conducted to ensure that any variation / discrepancies previously reported are being corrected during further production and that a satisfactory quality standard is being achieved.
Final Random Inspection (FRI)
This is the final inspection and is done when goods are ready for shipment. This inspection is conducted by at least two quality control officers, one of who has not been associated with the order before this inspection. This ensures an unbiased report.
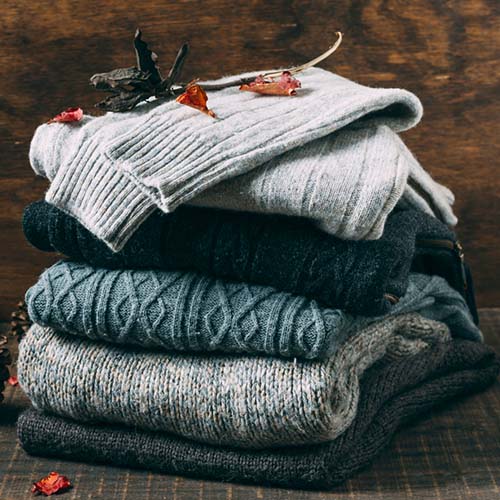
Please click the link to download the Company profile